A Closer Look at the PCB Fabrication Process and What You Should Know about It

Printed circuit boards, or PCBs, are at the heart of almost every electronic device in existence today. From clocks to calculators to IoT devices to your car, there’s a PCB powering things and helping to ensure functionality. PCBs serve important roles, primarily in two ways. First, they provide a physical home for important components that help control the device or system. Second, they route power to those components, as well as to the device in question.
To distribute electricity, PCBs are made with a series of copper wires (called traces) that connect components and allow electrons to flow. Understanding PCB fabrication is important, whether you’re teaching students the basics of electronic device operation or you’re designing the next hit Internet of Things device. In this guide, we’ll explore some of what you need to know about PCB fabrication.
On top of the base material, copper is laid, either as a full layer, or as a foil. Over that, a film is placed. This film has a photograph/image of the completed circuit. The film is exposed to light to detail the traces and component mounting locations, creating what is called a photo-resist. This is then placed in a developer solution that removes any unneeded material.
The next step in the PCB fabrication process is to use ferric chloride to etch the area without copper. If the ferric chloride solution is too strong, or if the PCB is left in the solution for too long, damage may occur, so timing and proper solution mixing are both critical considerations.
Note that this is just one option when it comes to PCB fabrication. There are other methods that do not rely on ferric chloride at all. For instance, milling machines are able to remove copper from the areas where it is not needed without damaging the underlying board. Another option is to use inks that resist the etching solution rather than a film.
At AdvancedPCB, we have decades of experience working with clients ranging from individuals to international corporations. We can help with prototyping, design, testing and offer full PCB fabrication services with minimal lead time and highly flexible minimum order requirements. Contact us today to learn more about how we can help.
To distribute electricity, PCBs are made with a series of copper wires (called traces) that connect components and allow electrons to flow. Understanding PCB fabrication is important, whether you’re teaching students the basics of electronic device operation or you’re designing the next hit Internet of Things device. In this guide, we’ll explore some of what you need to know about PCB fabrication.
Types of PCBs
Today, there are three types of PCBs manufactured. The PCB fabrication process is similar for each, although the more complex the board, the more complicated the fabrication process will be. The three types you’ll find today include the following:- Single – Single-sided PCBs are the simplest of the lot and are made with an FR4 base and a rigid laminate made from woven glass epoxy. One side of the laminate is covered with copper, while the other side is left uncovered. The copper layer can be of varying thickness to suit the usage needs and design of the board.
- Double – Double-sided PCBs use the same epoxy as single-sided PCBs. The primary difference here is that both sides have copper added so that traces can be etched. Each side has the potential to either act as a separate circuit board, or to integrate with the other, creating a more compact form factor for what would be a larger board if it were only single-sided.
- Multi-Layer – Some PCBs have multiple layers. They begin with the same substrate material, but use copper foil instead of a copper coating. Foil and base material are interleaved to create a sandwich effect that allows multiple layers of functionality.
Design
The first step is to design the PCB. Usually, you’ll use design software, such as PCB Artist, which is a free, full-feature tool that delivers powerful capabilities and ease of use. During this process, you lay out the board, indicate where components go, route traces, add capacitors, and more. However, this is all theoretical. No actual PCB fabrication occurs during this stage – it’s all about planning, prep, and basic testing for functionality.The Design and Fabrication Process
With the design work out of the way, you now need to choose the bare PCB boards and create the traces. This process will remove unwanted/unneeded copper, leaving you with the characteristic thin lines to carry current from component to component. In most cases, a chemical etching process is used – ferric chloride is the most common etching agent, although there are other agents, and even other etching processes that may be used.On top of the base material, copper is laid, either as a full layer, or as a foil. Over that, a film is placed. This film has a photograph/image of the completed circuit. The film is exposed to light to detail the traces and component mounting locations, creating what is called a photo-resist. This is then placed in a developer solution that removes any unneeded material.
The next step in the PCB fabrication process is to use ferric chloride to etch the area without copper. If the ferric chloride solution is too strong, or if the PCB is left in the solution for too long, damage may occur, so timing and proper solution mixing are both critical considerations.
Note that this is just one option when it comes to PCB fabrication. There are other methods that do not rely on ferric chloride at all. For instance, milling machines are able to remove copper from the areas where it is not needed without damaging the underlying board. Another option is to use inks that resist the etching solution rather than a film.
Drilling Holes/Vias
Numerous holes, or vias, must be drilled through the PCB during the fabrication process. These are used for a couple of different things. One is obvious – mounting components by their pins. However, another is to ensure that the individual layers of the board can be lined up. This is particularly important with multilayer PCBs.Soldering and Silk-Screening
The final two steps of the PCB fabrication process are soldering and silk-screening. A soldering mask is put in place over the PCB to protect the copper from damage and to ensure that soldering is done accurately. Then, the board is flipped over and names, numbers, symbols, part identification information, and other text elements are silk-screened onto the board.Decades of PCB Manufacturing Experience
In the end, PCB fabrication is a complex process. Accuracy and proper planning are essential from the very beginning. Whether you’re designing your first PCB ever or you’re hard at work on yet another prototype, it pays to have the right PCB design software, as well as the right manufacturing partner.At AdvancedPCB, we have decades of experience working with clients ranging from individuals to international corporations. We can help with prototyping, design, testing and offer full PCB fabrication services with minimal lead time and highly flexible minimum order requirements. Contact us today to learn more about how we can help.

AdvancedPCB
Related Posts
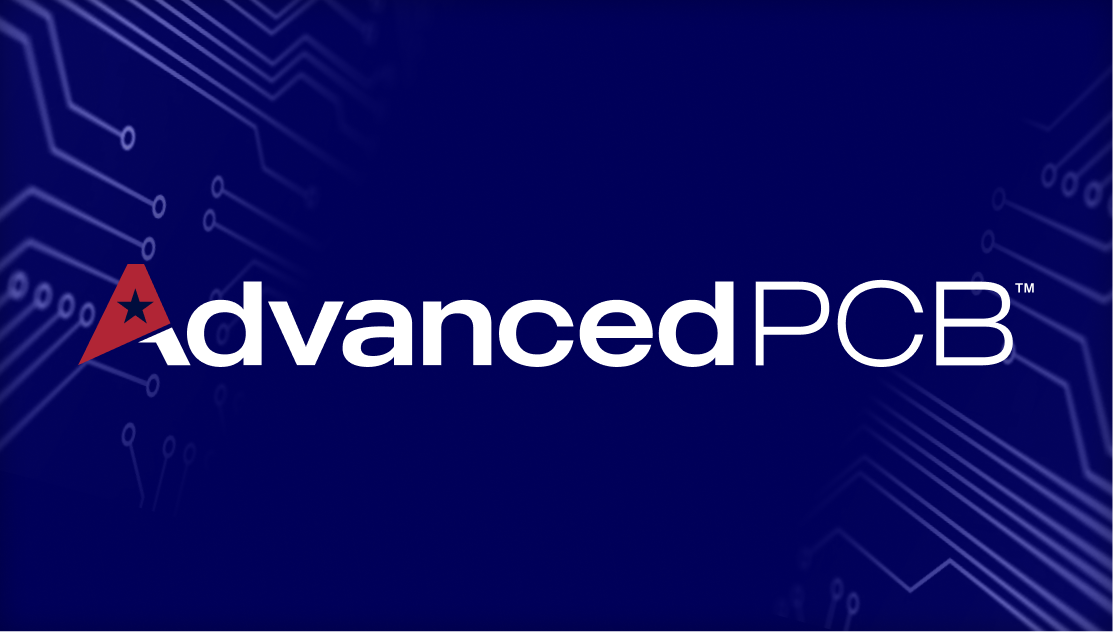
Future trends of the circuit board
As consumer demands for faster, smaller and more efficient devices intensify, so do printed circuit board requirements. PCBs are the backbone of all electronic devices. They affect their size, speed and functionality.
Future trends of the circuit board
Read More
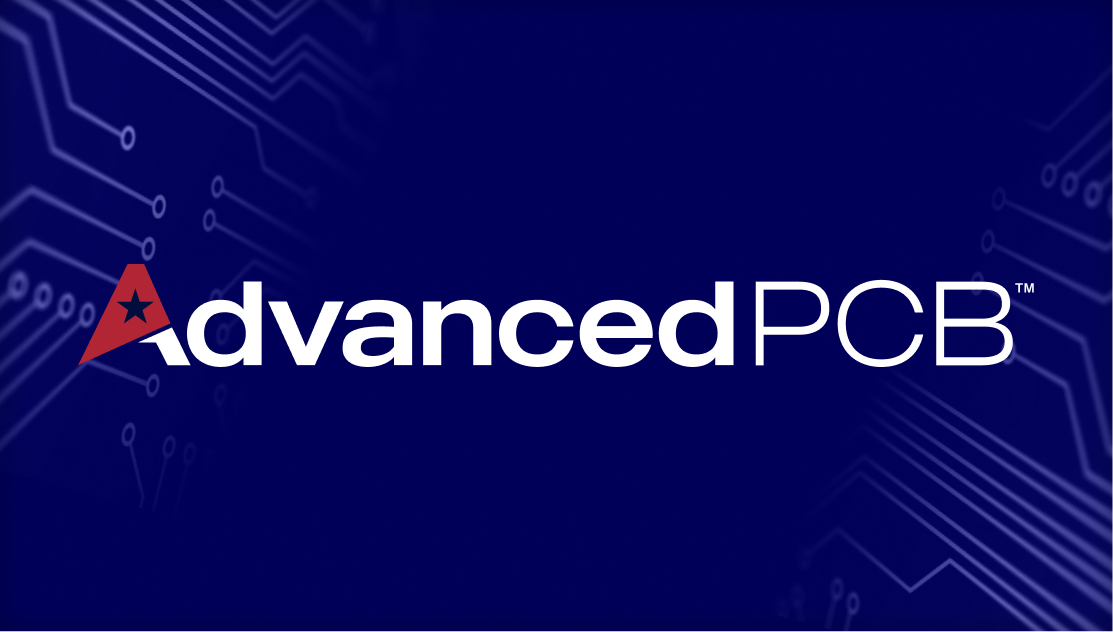
Understanding the Difference between PCB prototyping and Full Spec Production
Printed Circuit Board manufacturers such as AdvancedPCB offer two main types of services- Printed Circuit Board Prototyping (PCB) and full spec production. But what exactly do these mean, and what does each have to offer?
Understanding the Difference between PCB prototyping and Full Spec Production
Read More

Trends in Circuit Board Design
The circuit board has been with us for a very long time at this point. It’s tempting to think that because they so closely resemble the generations that came before, today’s circuit boards are not all that different from what they once were. However, from the materials available to heat resistance, from transfer rates to size, circuit boards have evolved a great deal over time.
Trends in Circuit Board Design
Read More
Browse
All Categories
Recent Posts
View Recent Posts