Benefits of Multilayer Printed Circuit Boards | Blog

Most PCB manufacturers are finding the demand for multilayer boards increasing by leaps and bounds. This growing demand is fed by the need for smaller, lighter boards for use in electrical devices, military equipment, healthcare miniaturization, and an expanding market for smart devices incorporated in home automation systems.
Smartphones and computers are perfect applications for multilayer PCBs with their need for compactness and light weight, yet sophisticated functionality.
From a technical standpoint, there are numerous advantages to the use of multilayer designs, over and above saving space and weight:
- By incorporating multiple layers in a single PCB, boards can increase functionality.
- Manufacturing processes for multilayer boards result in high-quality, reliable end products.
- Multilayer boards by their innate electrical properties provide high capacity and high speed in a smaller footprint.
- Higher density of assembly
- Connectors required for multiple separate PCBs are reduced or eliminated, simplifying construction and further reducing weight.
- Multilayer PCBs can be manufactured in both rigid and flexible construction. Be advised though, that the more layers incorporated in a flex PCB, the less flexible it becomes.
Downsides of Multilayer PCBs
Every technology has pros and cons, and multilayer PCBs are not immune from negative attributes:
- Cost – one of the primary negatives in designing and implementing multilayer PCBs is the cost. As specialized processes are involved in the manufacturing of these boards, there is a considerable investment required for fabricators to offer these services. This makes the cost of multilayer boards higher than a traditional single or double-sided board.
- Service availability – not all PCB manufacturers have made the commitment to manufacturing these complex boards, limiting the resource options available to PCB designers.
- Compactness of multilayer boards generates design concerns for such issues as crosstalk and impedance problems.
- With increased functionality comes the need for more extensive testing of a single PCB. Manufacturing cycles may also be longer, due to the very complexity of the manufacturing process.
- Repairing a multilayer PCB can be extremely difficult, and may even be unfeasible or impossible. This makes failure of a multilayer board costly, since it may need to be totally replaced.
- Interconnection between layers is critical for board function, making design and fabrication of microvias and overall density critical.
Processes for Manufacturing Multilayer PCBs
Due to the sheer demand for multilayer PCBs for use in technology devices, healthcare equipment, military use, and even such consumer products as smart televisions and home monitoring equipment, most competitive manufacturers have positioned themselves to respond to the need for these boards. There remains a mix of capabilities among fabricators related to volume production capabilities, and the number of PCB layers that can be produced.
Manufacturing of multilayer PCBs involves a process of combining alternating layers of prepreg and core materials into a single unit, utilizing heat and high pressure to ensure uniform encapsulation of conductors, elimination of air between layers, and proper curing of adhesives that bind the layers together.
Due to the multiple layers of material, execution of drill holes among layers must be carefully observed and registered. It’s important for successful manufacturing of multilayer PCBs that engineers incorporate symmetrical layout across layers, to help avoid twisting or bow in the materials when heat and pressure are applied.
When sourcing a fabricator for multilayer PCBs, it is critically important to acquire the manufacture’s capabilities and standard tolerances for these complex boards, and utilize design for manufacturing (DFM) techniques to accommodate those standards. This goes a long way toward building confidence that the result will meet all functional, reliability, and performance expectations.

AdvancedPCB
Related Posts
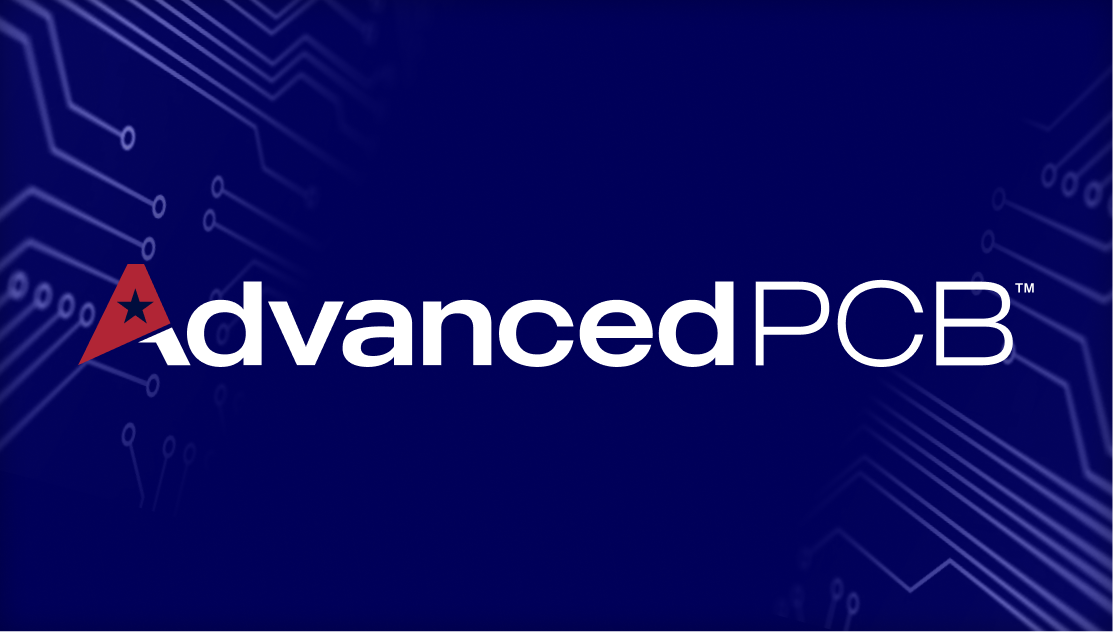
Future trends of the circuit board
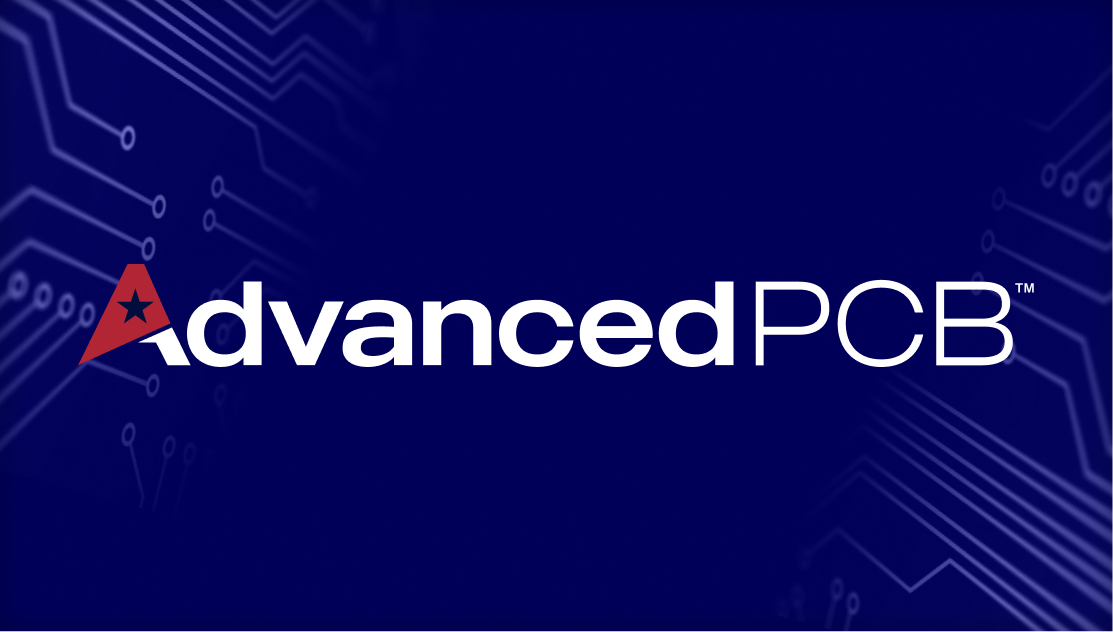
Understanding the Difference between PCB prototyping and Full Spec Production
