High Density Interconnected PCBs (HDI)

What Is Different About HDI PCBs?
High Density Interconnected printed circuit boards (HDI PCB) have made technological advancements in electronics possible. They have been referred to under a variety of names: Sequence Build Up (SBU), Microvia Process (MVP), and Build Up Multilayer (BUM) boards, to name a few. Eventually the IPC (Association Connecting Electronics Industries) adopted the HDI term for consistent terminology across countries and industries.
HDI PCBs possess technical characteristics of extremely high density routing interconnections and make high density of components possible. These attributes contribute to the high performance and light weight of HDI boards that make them ideal for powering today’s devices. HDI PCBs are a perfect solution for the shrinking footprint of electronics technology, comprising the core components of such technical marvels as laptop computers, tablets, smart phones, and even wearable technology such as fitness bands and virtual reality devices.
Why Utilize HDI PCBs?
HDI boards have many technical and physical advantages over traditional through-hole or even standard surface mounted technology (SMT) boards:
- Size – by sheer technical characteristics, HDI boards can accommodate more connections in the same size printed circuit board for a more dense PCB with a lower number of layers.
- Design advantage – HDI provides the designer with more flexibility through increased capacity on the board that contributes to faster signal processing.
- Reliability – IPC studies refer to superior reliability offered by small-blind vias over through-hole (TH) vias due to the greatly reduced aspect ratio (AR).
- HDI is practically the only option where more complex and dense packages such as those with high pin counts and a very low pitch are incorporated.
- Demand for smaller boards – manufacturers need increasingly smaller and lighter boards with more functionality. Non-HDI boards require more space and weight, making HDI technology the obvious choice.
- Functionality – with HDI, multiple traditional PCBs can be integrated into one HDI PCB.
- Signal integrity – improved electrical performance and higher signal integrity requirements are attributes provided by HDI technology.
Design Requirements for HDI Boards
HDI technology brings its own set of specific design concerns:
- Material choice – all PCB design takes material and component selection into account, but for HDI there are unique manufacturing constraints that come into play. Materials selected will impact the electrical performance of signal traces and certainly the cost of the end product.
- Micro via stacking – effective designs can take advantage of HDI benefits in stacking micro vias as opposed to staggering.
- Every Layer Inter-Connection (ELIC) – this technique now popular in smart phone construction provides smaller pitches and the elimination of mechanical holes inside the board, which consumes space.
- Distribution of blind and buried holes. Asymmetric design of stacks can result in uneven pressure, causing warpage of boards.
- Component layout – the very density of HDI technology requires close attention to placement to ensure viability in soldering, installation, and maintaining boards. This will facilitate any necessary rework by allowing the maximum space tolerances while still taking advantage of the available density.
- Track uniformity and minimum line width. These factors are important considerations to avoid open and short circuit conditions.
When formalizing HDI designs, the most constant concerns are still cost and quality, which are echoed as the primary concerns of consumers when purchasing the devices containing the boards.
Thoughts When Considering HDI Use
There are additional points to consider before implementing HDI in PCB designs:
- Skill set – planning PCB functions are quite different for HDI PCB designers. The high density, layer consideration, and manufacturing complexity are all factors that need to be planned out before a PCB is sent to a fabricator. Problems with designs after manufacturing has begun are costly, and may result in a complete redesign and scrapping of any boards already produced.
- Planning – major changes in PCB layout or function is extremely difficult in HDI boards, making accurate design processes critical to cost-effective manufacturing. Planning design carefully will promote successful production and functionality of the boards and keep the project within budget.
Each of these points emphasizes the need to consider design for manufacturing (DFM) tools and processes. It is equally important to seek advice and design recommendations from the fabricator that will actually produce the HDI boards before manufacturing begins.

AdvancedPCB
Related Posts
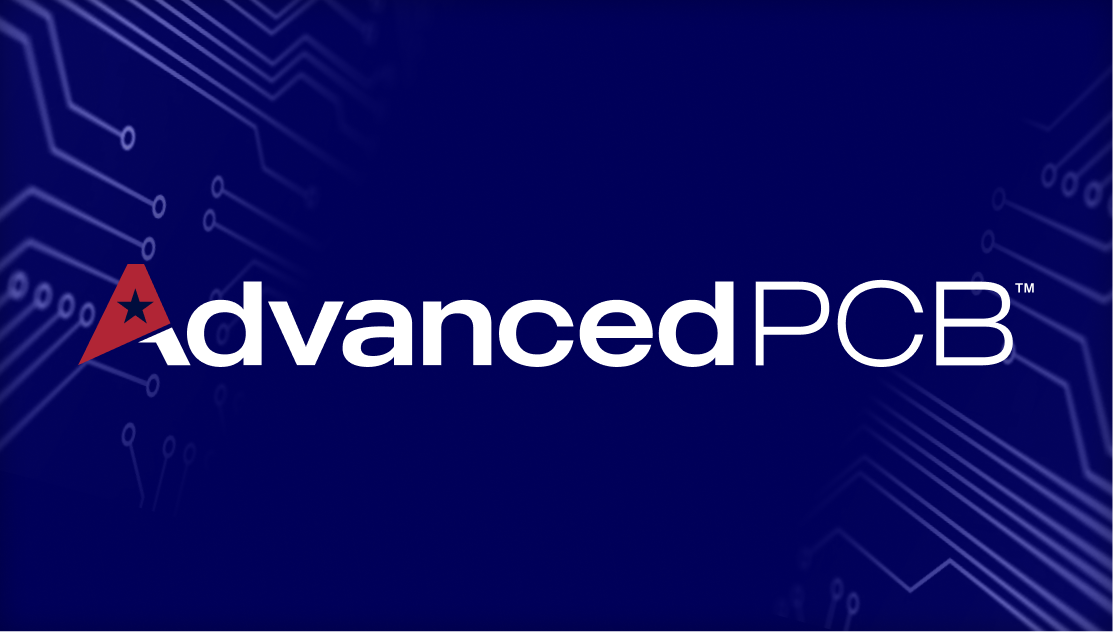
Future trends of the circuit board
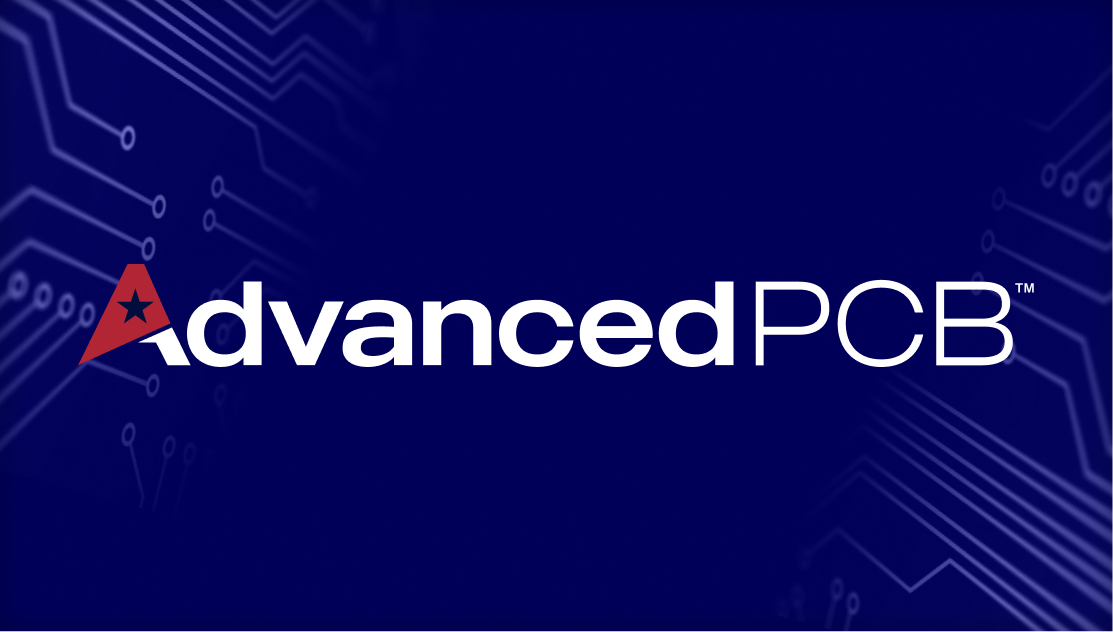
Understanding the Difference between PCB prototyping and Full Spec Production
