How Are PCBs Made?

It wasn’t that long ago that PCBs were made out of cardboard with only one-sided capabilities. Nowadays, though, PCB manufacturers are innovating ways to make PCBs smaller, more durable, and able to pack in more electrical power. These changes, over time, have enabled PCBs to make their way into everyday electrical consumer products. The use of a PCB is ubiquitous in today’s society, which has sparked whole fields of electrical engineers and hobbyist tinkerers to create more complex designs.
The process of PCB fabrication is impressive, and even those familiar with PCB design might not know all the ins and outs of how PCBs are made. Learn more about the different PCB fabrication techniques that make your design go from the virtual image on your computer screen to the tangible, green board in your toaster.
The Basics
Before diving into PCB fabrication, it’s important to know what makes up a PCB. Often, people will describe PCBs as a layered cake. The most basic PCB designs have four layers: the substrate (base), copper, solder mask, and silkscreen. These layers all work together and must be in total alignment for the final product to work.
Once you’ve designed a PCB and sent your PCB design off to the manufacturer, what will they do with it? For starters, they use your PCB design as the blueprint for the entire process.
Through-Hole Method
One of the earliest forms of PCB fabrication was the through-hole method. This tried-and-true method is quickly being replaced by a more modern PCB fabrication, known as surface mount technology (SMT). While each has its advantages and disadvantages, SMT PCB manufacturers seem to be able to produce smaller and cheaper PCB boards.
We’ll take a look at the intricate work that goes into a through-hole PCB design first. The most significant difference of the through-hole method is that manufacturers drill a hole into the board so that factory workers can double-check that each layer is aligned before moving onto the next step. With the through-hole method, manufacturers will print your PCB design onto special laminate paper. The manufacturers can attach a thin sheet of copper once the design is captured onto this special paper. This will be the basis of your substrate, or the base of the PCB.
Creating Layers
The next step is to start working on the copper that will form the layers of your PCB. This process is a bit similar to how photographs are developed – to the point that at-home PCB makers will use the same processing chemicals. Essentially, the special laminate paper is covered with photo-reactive chemicals, and when a UV light passes over it, it hardens the desired areas. This shows manufacturers which parts, based on your design, should be kept for the final PCB board and which bits of copper should be chipped away.
When the chemicals dry and harden, the board is washed in an alkaline solution and is ready to be inspected. If the board is good to go, a technician uses a powerful chemical to remove unnecessary copper, leaving behind only the copper needed per your PCB design.
Next, the copper layers are laminated together. Technicians must keep a keen eye for detail and always watch that each layer is perfectly aligned with the last. The result is a beautiful, half-finished board.
Factories can use an x-ray machine to uncover where the holes are meant to be drilled and then use a high-powered drill for precise execution. The board is finally plated, and the layers are fused with a series of chemicals. There is one last etching that occurs before the solder mask is attached. This etching ensures that your PCB has the right connections to make your creation function.
Surface Mount Technology
Surface mount technology (SMT) has become more commonplace in the PCB fabrication process because it allows for easier mass production. With an SMT outfit, the PCB fabrication process is more automated and thus less prone to human error. SMT-designed PCBs also do not have the same hole that is prominent in the through-hole method. Here’s a brief glimpse into how these PCBs are produced.
Simple As a Stencil
By using high-powered computers and technology, machinery takes your PCB design and creates a stencil. The stencil contains all the information the automated process will need to finish up your design. The stencil also allows machines to trace solder paste onto the board only in the designated areas.
The board is now ready to run through a pick-and-place machine, which takes the guesswork and error out of the PCB design process. The pick and place machine holds various components in their reels and reads the solder paste to place the proper components onto the board as directed by the PCB’s design. The solder paste will also hold everything in place so that components cannot be knocked off-kilter, thus resulting in a faulty product.
Once this process finishes, the PCB is heated and melts the soldering paste so that the layers meld together. The PCB is then ready for a clean-up, to ensure there is no residual solder paste on the board. At last, the board will receive an inspection of any potential defects.
Advantages of Surface Mount Technology
As you can see, SMT is a much more straightforward and more automated process. Its simplicity is what makes it best for the mass production of PCBs. Once a stencil is created for a design, you can print countless boards. Since the process relies on computers and machines rather than technicians, it’s also less vulnerable to human error. If there’s a mistake with a PCB board, it’s likely because the pick and place machine needs some reconfiguration.
Another big advantage of SMT fabrication is that they tend to allow for higher density component placement while still maintaining smaller boards. Since the board is smaller, the connections have a shorter distance to travel for better power.
The most significant disadvantage of the stencil-based process is that it makes it more challenging to produce prototypes quickly. This system works best if the same stencil is being used repeatedly, rather than creating one stencil that will change.
However, given the automation of the SMT process, it’s no wonder that the SMT fabrication method has gained greater momentum in the PCB world than the through-hole. Whichever route you go, make sure you’re aware of the PCB fabrication process that your manufacturer uses. In today’s world of making everything faster and smaller, you’ll want to make a decision that gives you the best return on investment.

AdvancedPCB
Related Posts
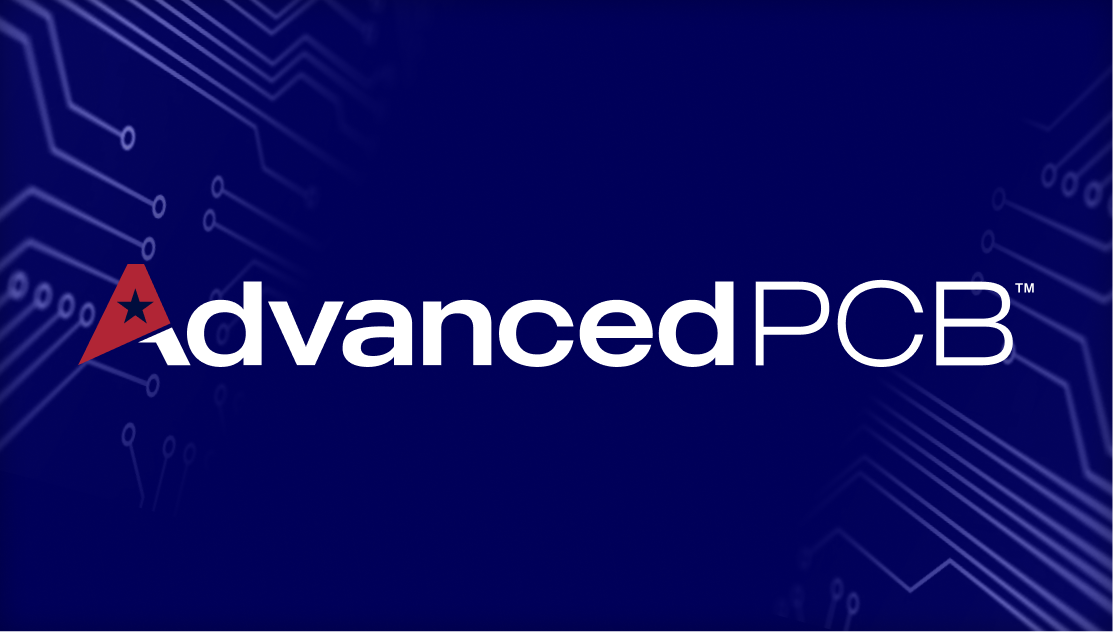
Future trends of the circuit board
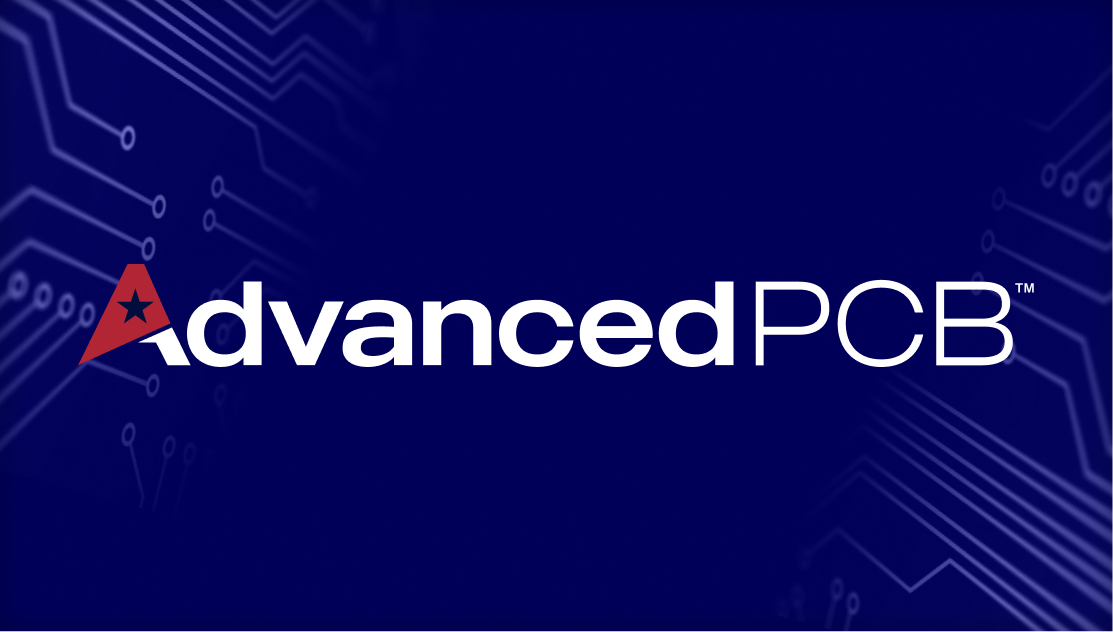
Understanding the Difference between PCB prototyping and Full Spec Production
