Laser Direct Imaging in PCB Manufacturing

How Does LDI Work?
LDI processing requires a board with a photosensitive surface, positioned under a computer-controlled laser. A computer scans the board surface into a raster image. Matching the raster image to a pre-loaded CAD/CAM design file that contains the specifications for the desired image intended for the board, the laser is used to directly generate the image on the board.
Changes to the desired image now become a matter of updating the design file, which can be done more consistently and cost-effectively than traditional photo methods.
Advantages of LDI over Photo Processing
Traditional photo processes requires multiple steps to create the phototool used to generate the image on the PCB. This has generated a number or challenges for PCB fabricators over the years. LDI provides a number of advantages:
- Quality – photo film issues in the past have resulted in imperfect images due to inherent susceptibility to fluctuations in temperature or humidity. Laser images result in much more precise and consistent images, and eliminate any film-related defects.
- Laser imaging provides precise positioning and improved resolution. Image lines, spaces, and alignment are more accurate.
- Photo methodology requires temperature and humidity controlled environments to provide the most accurate transfer of images to boards. LDI reduces the impact of environment on the resulting images, and removes the impact of light refraction inherent with photo processing techniques.
LDI fabrication offers specific advantages where short runs or quick turn-around are required, making creation of artwork and setup of phototool methods impractical. LDI is also an important factor when close tolerances and tight registration are involved.
Today’s customer demands for smaller, lighter, high-density PCBs are quickly edging out photo technology as a practical tool in generating PCB images.

AdvancedPCB
Related Posts
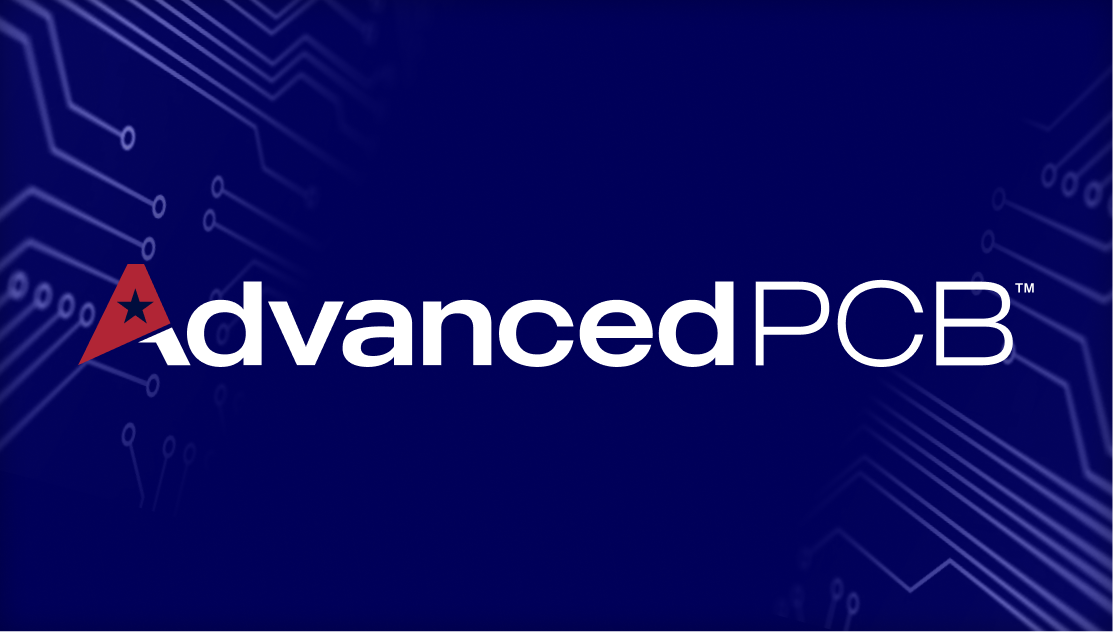
Future trends of the circuit board
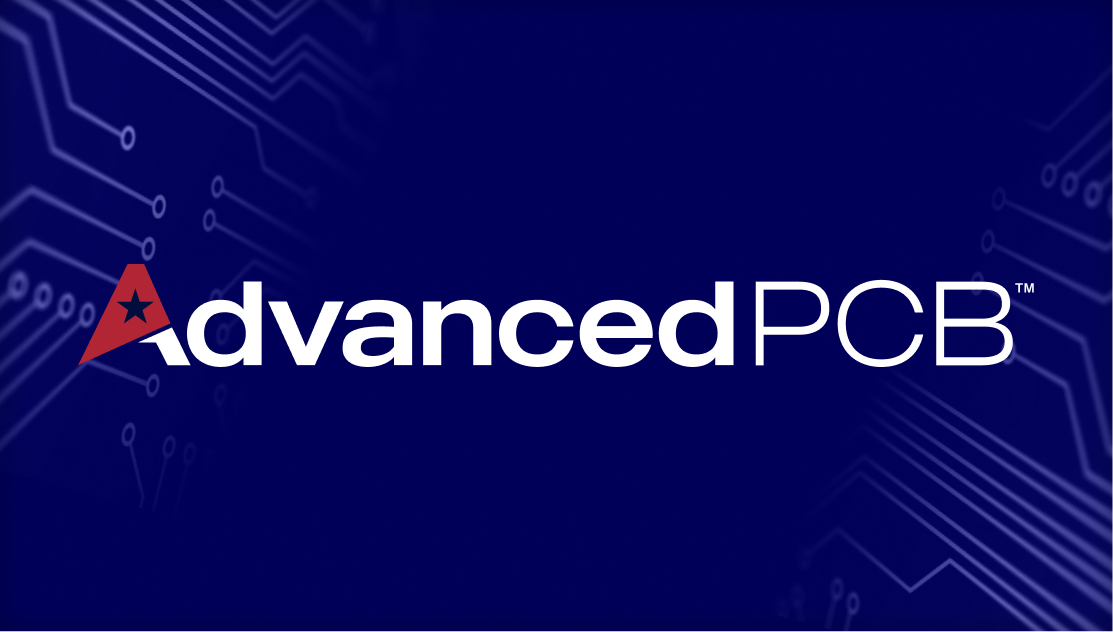
Understanding the Difference between PCB prototyping and Full Spec Production
