PCB Mistakes and How to Avoid Them

PCB Mistakes Are Not Uncommon
Printed circuit boards (PCBs) are becoming more and more complex while at the same time more critical to technology. PCBs are a basic building block of not only computers and high-tech communications equipment, but are found in every automotive vehicle, smartphones, lighting systems, and even children’s toys.
As PCBs become more sophisticated and miniaturized, design engineers are challenged to keep up with the evolution of available materials, design and layout software, and manufacturing capabilities. It’s small wonder that there are many opportunities for making mistakes in the development of PCBs.
When avoiding common PCB design mistakes, it’s important to look for:
- Layout issues such as missing traces or vias, incorrect sizing of traces or pads, and noise generation.
- Schematic errors that result in performance issues or total functional failure. With smaller footprints required for some PCBs and multi-layer boards it becomes much easier to generate layouts that will encounter difficulties during manufacturing or during testing.
- Failures due to environmental issues. Designers need to be aware of the anticipated environment their designs will be exposed to, and plan materials and layout accordingly. Every condition the end product will be exposed to should be evaluated for PCB potential failure or conditional issues.
- Not using available tools. Electronic Design Automation (EDA) tools are widely available, but they are not all created equal. Evaluate the available applications to determine which best suits the PCBs to be designed. Design tools can improve layout design and generate all files needed for fabrication of the boards.
- No review process. Lack of communications between the electronics engineer and PCB designer (when they are different technicians) can result in boards that do not function as the engineer planned.
- Test planning. A prototype board may pass initial testing for base functionality, but failures can occur when board moves into production and gets installed in the final product. This is a poor time to discover that the PCB does not perform well (or at all) in certain settings. Costs of rework and product recalls become extremely expensive at that point.
- Missing files. It’s not uncommon for manufacturers to come back to designers related to files that are not complete or which may not be labeled/named clearly for them to identify the files for fabrication. This results in faulty boards or manufacturing delays.
- Lack of familiarity with manufacturing requirements. Even the most carefully-designed circuit with the most advanced technical design may not be efficiently manufactured if the designer does not understand the fabrication process. This could include dimensional tolerances that are outside what is necessary, resulting in manufacturing complexity that can increase costs or even alter the footprint of resulting boards.
Avoiding Common PCB Design Mistakes
Many common PCB mistakes can be easily avoided or at least reduced by implementing some standard procedures and best practices:
- Even the most savvy design engineer can make a mistake – often one that could be readily detected by a second designer. Initiating peer reviews can help capture at least some of these design errors or at least raise questions that may point out design flaws or missing notes and documentation that can result in manufacturing delays.
- Use the sophisticated tools available for design and PCB layout, and learn to use them effectively. Training in using design tools properly can avoid unintentional errors in layout or manufacturing specifications. Do not underestimate the value of thorough training.
- Design for manufacturing. Available layout design software applications have improved by leaps and bounds in recent years, yet it’s only as good as the software developers. Final designs generated by layout design software may provide what appears to be a workable PCB, yet when it gets to the fabricator there may be issues that make the design difficult or even impossible to manufacture. To avoid such issues, implement procedures to utilize design for manufacturing (DFM) software before the design is sent out for manufacturing of the prototype or final product. Such applications detect likely manufacturing issues, missing files, and much more.
- Utilize saved templates. By setting up standard templates that all designers have access to, designs can be completed in a more timely basis with fewer concerns for omissions and obvious errors.
- Collaborate with fabricators. By developing a relationship of good practices and consistent communications with PCB manufacturers, design engineers can resolve problem areas in the least possible time and with the lowest impact on board cost due to early detection.

AdvancedPCB
Related Posts
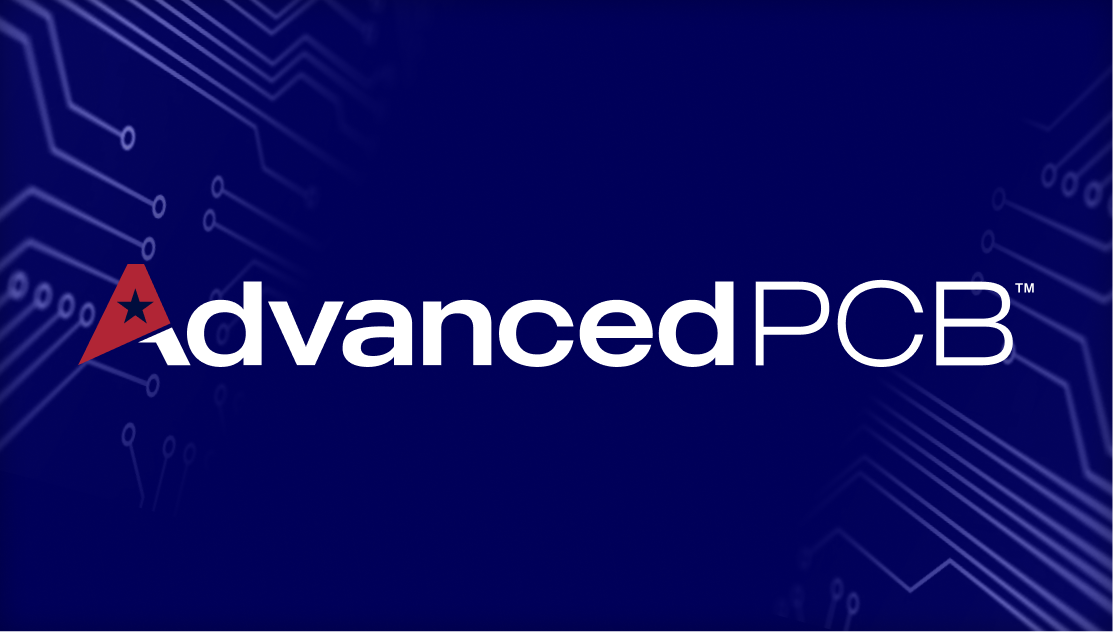
Future trends of the circuit board
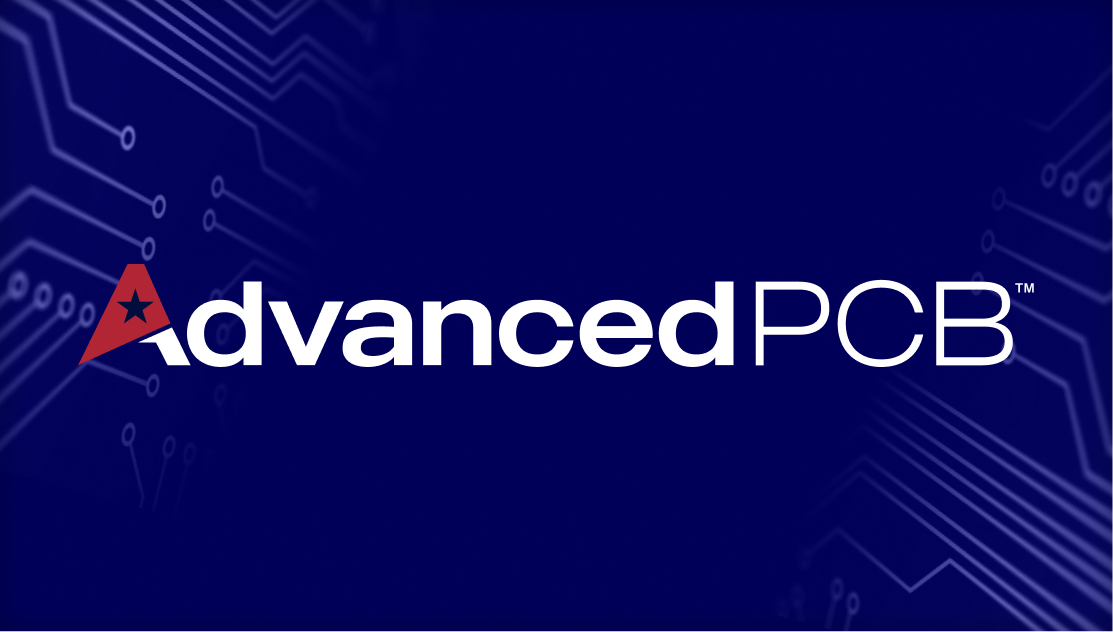
Understanding the Difference between PCB prototyping and Full Spec Production
