Tech Talk For Techies: Highly Reliable Via-In-Pad Design

Via-In-Pad (VIP) is rapidly becoming more commonly used in modern printed circuit design due to many considerations, including the need to miniaturize the PCB form factor. This review of via-in-pad technology can help remove some of the mystery of VIP in PCB manufacturing.
Via-In-Pad Structure Types
Pad diameter is the major factor in the device footprint that will determine what type of VIP structure is utilized; drilled-and-filled or laser microvia. In order to meet the minimum annular ring requirement of IPCClass 2 or Class 3 there must be sufficient pad size to accommodate the via diameter and allow for manufacturing tolerances.
Mechanically Drilled/ Epoxy Filled Vias
The available range of finished hole sizes for epoxy filled vias (mechanically drilled) is a minimum 0.008″ through a maximum of 0.018″. To consider the minimum finished hole size (FHS) of 0.008″ you must consider the pilot drill diameter (drill size before plating). A pilot drill diameter for 0.008″ FHS will be 0.010″, which will now determine the minimum pad size as defined by minimum annular ring.
Laser Drilled Microvias
Microvias require as little as 0.002″ annular ring (laser via diameter + 0.004″). Laser microvias have the advantage of not only being smaller in diameter than mechanical drills (0.003″ to 0.006″ typical diameter for PCB designs), but they have the ability to register much better as the process assures alignment to the sub-layer and the overall hole pattern will scale to match the sub-layer image in X and Y dimensions.
BGA Requirements
With BGAs, footprints with 0.5mm and less require microvias as the pad diameter is not large enough to accommodate mechanical drills. Microvias most commonly span a single dielectric thickness–ideally one half deep as the diameter (0.5:1 aspect ratio) with an a maximum depth equal to the diameter (1:1 aspect ratio). This is due to the fact that the fully copper plating process takes a substantial amount of time and is not designed to fill deep, blind holes that extend down deep into the board.
Do you have questions about VIP? Learn more here in our full discussion of the topic. You may also wish to discover more about this and AdvancedPCB's full range of PCB manufacturing and assembly capabilities. For over 25 years, AdvancedPCB has provided its customers in the high tech aerospace, military (DOD contracts ready), medical, and commercial industries with printed circuit boards that deliver powerful performance, reliability, and precision for critical applications. AdvancedPCB's over 10,000 customers rely on the highest quality standards they receive for all PCBs, from simple prototypes to complex designs requiring microvias and machining.

AdvancedPCB
Related Posts
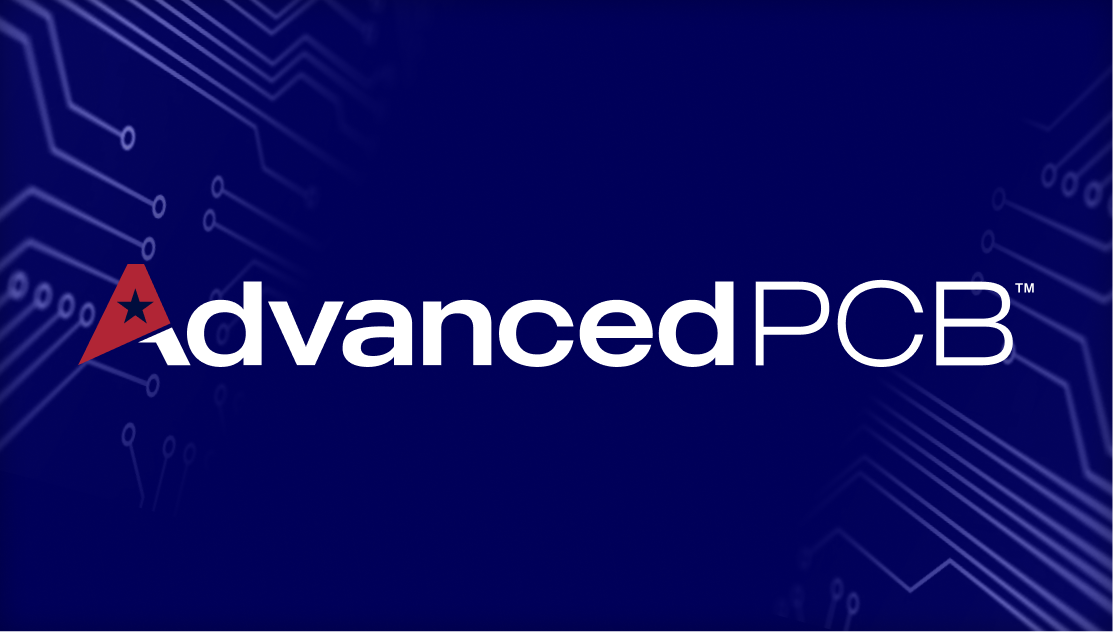
Future trends of the circuit board

2-Layer vs. 4-Layer Printed Circuit Boards
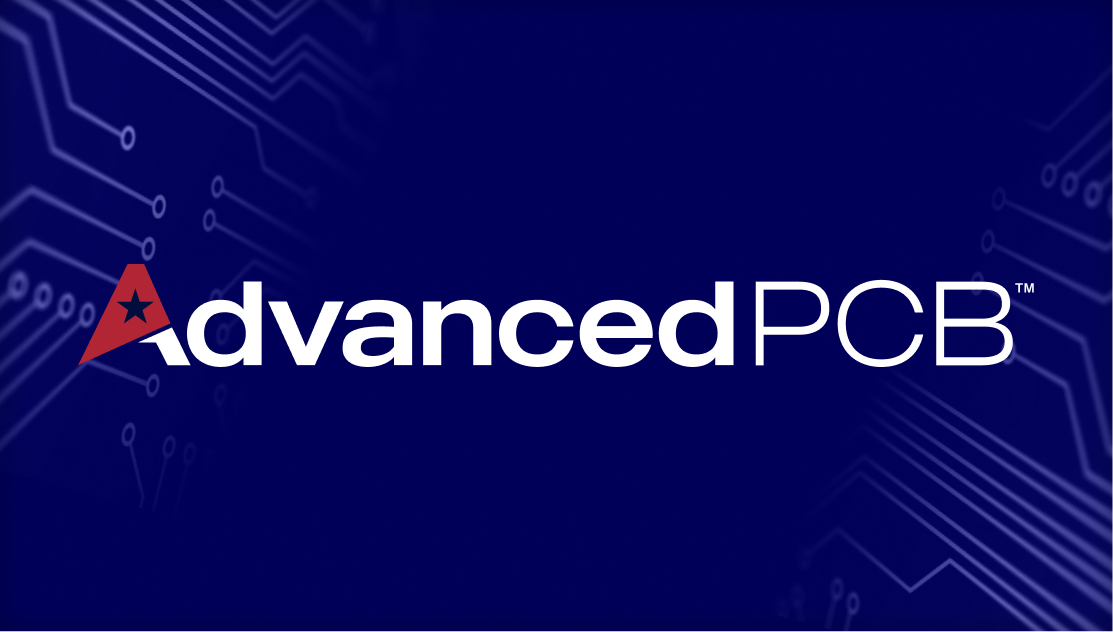