The Benefits of PCB Panelization

.jpg?lang=en-US)
During the printed circuit board production process, ensuring that each board is uniform is essential. Without uniformity, some boards may not meet the requirements of its intended application and will therefore be discarded. As circuit boards become smaller, changes to production processes must be made in order to ensure that quality is not sacrificed. PCB panelization helps to address these issues by keeping smaller boards attached to one another in a larger array. Doing this increases throughput and allows the manufacturing process to maintain its standard panel size. In addition, PCB manufacturers can use existing fixtures and equipment to keep efficient handling of boards high. Finally, smaller PCBs run the risk of being removed during routing due to the pressure used by the router’s vacuum. The risk of this is reduced with panelization, allowing designers to get the volume of boards they need quickly without added headaches.
The PCB Depanelization Process
Depanelization is the removal of the PCBs from the panel itself. The depanelization process occurs before final assembly and testing takes place. This can be done either with a mechanical or laser routing and each has its benefits. Laser routing is an effective method because it provides accurate tolerances. Mechanical routing may be more cost-effective, but it also creates much more debris along the way. As a result, your circuit boards may need additional cleaning after depanelization before they are shipped. It is important as a designer to specify and assembly requirements in your design files and order to ensure expediency and that all of your needs are met. Discuss your options with a representative at AdvancedPCB and place your PCB order today.

AdvancedPCB
Related Posts
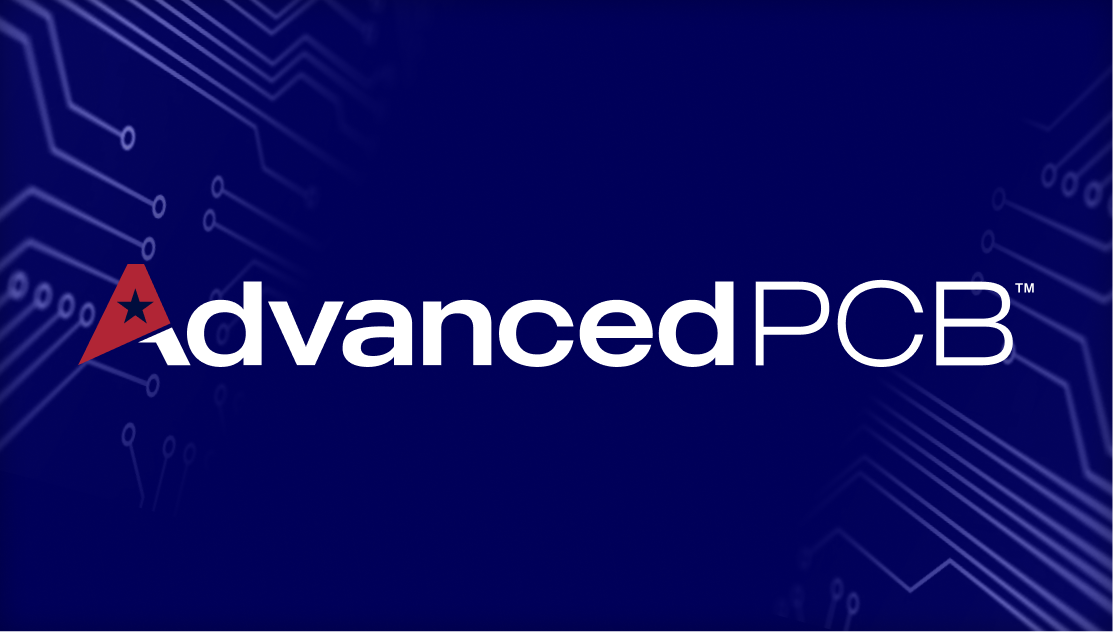
Future trends of the circuit board

2-Layer vs. 4-Layer Printed Circuit Boards
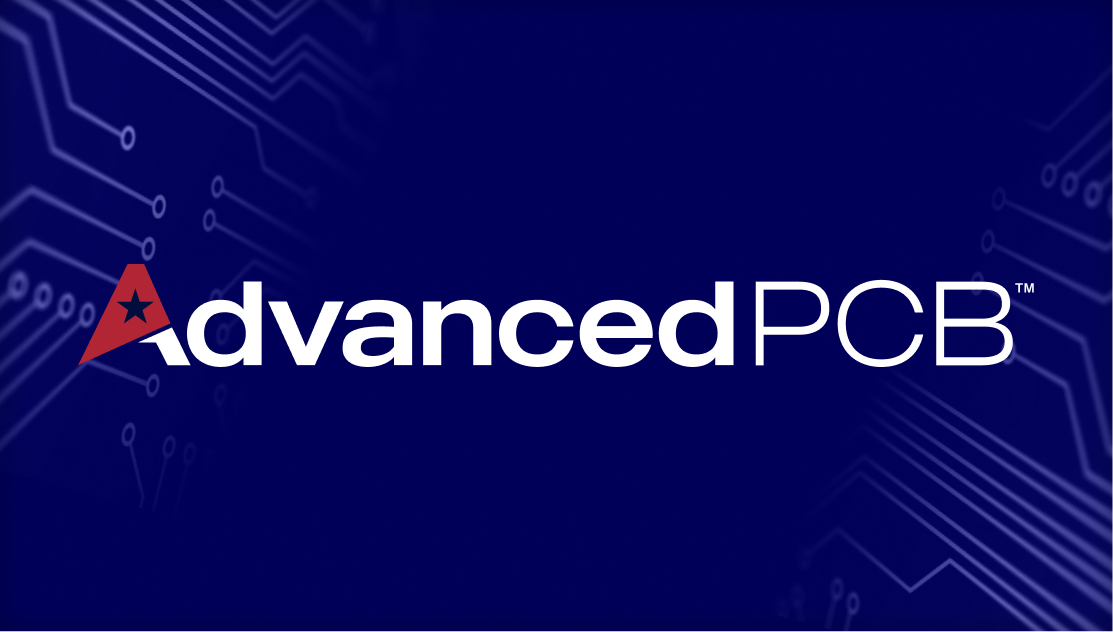